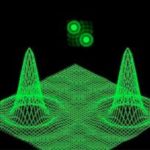
Figure 1 – Classic Diffraction Patterns
Sampling theory and filtered pulse responses have made these “Mexican Hat” curves familiar to a new generation of engineers – the concept of the Airy Disk is even older. In Figure 1 we see the classic diffraction patterns of light mapped into three- and two-dimensional domains. The main display is of an x-y plane given amplitude response in the z-axis. And shown at upper centre is the “bird’s eye view” which is also how the viewer perceives the scene with the undistorted x-y plane set to black level.
The preference for either interlace or progressive “scan” takes into account the mutual interference of these disk patterns. What the amplitude response can be and how finely the dot patterns are pitched together is at issue. Not surprisingly 720p and 1080i closely match in spatial expectation but not necessarily in amplitude and temporal dimensions.
Amplitude response is always an issue where a sensor supports all possible basic variants. There must be an aggregate of sub-pixels that can be conformed according to the preferred display format. For example the 1080 system demands an array of 1920H x 1080V pixels and a clock speed capable of transporting these. Clearly these numbers are greater than those for the rival 720 format but nevertheless they are the governing case affecting overall design. In practice sub-pixels are grouped into pixels because 1080 is not wholly divisible by 720.
The temporal domain cannot be ignored. Generally speaking a progressive format is deemed better at handling motion judder whereas an interlaced format handles fine detail well. It is a matter of adjusting the height and width of the Mexican Hat for the least annoying interference. However the nature of speed of movement within the picture is also critical, for example a football match with many camera whip pans differs totally from a motor racing event skillfully framed in tracking shots.
From the beginning of raster line scan television, interlace was preferred to reduce bandwidth just as the double-shutter technique of cinematography reduced the required film footage. If the future is with progressive formats then the penalty lies with costly bandwidth and increasing noise. Interlace remains attractive if the motion judder is not objectionable because horizontal resolution especially is higher and the finer “line” structure perceptibly improves the vertical dimension. Visual grammar of course changes as time passes and we can therefore expect viewers to become more discriminating with HD and 3D developments. Yet handle high symbol and bit rates without resort to excessive compression are problems not easily solved.
Once the issues of format dimensions have been decided, the practicalities of how to make it work with pictures invoke past techniques as well as future technology to create a new generation of charts and procedures. Despite the subtle differences the broad principles remain the same.